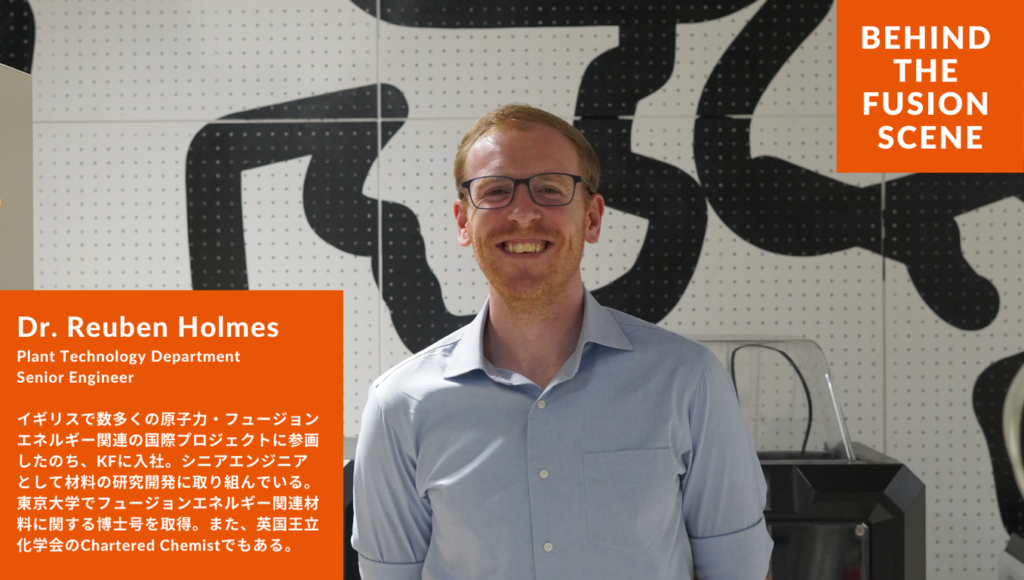
In a nutshell:
博士課程で研究を行う傍ら、2022年8月にインターンとして京都フュージョニアリング(KF)に入社し、材料に関する研究開発に携わったReubenさん。2023年10月からは正社員となり、これまで8年間、イギリスの原子力業界で携わったプロジェクトの経験を生かしてフュージョンプラントを作るうえで欠かせない材料の研究開発に取り組んでいます。
京都フュージョニアリング(KF)に入社した理由を教えてください。
KFに入社した理由は大きく2つあります。1つは、新しいことにチャレンジしたいと思ったからです。イギリスの原子力業界で化学者として8年間働いていましたが、そこからさらに幅広い知識と知見を蓄えて、研究者としてだけではなく技術者としても活躍したいと考えていました。
2つ目は、日本で生活してみたいという好奇心です。母国であるイギリスとは異なる環境に飛び込むことで、新たな自分を発見するとともにグローバルな視点を身に着けることで、もっと人間としても成長できると信じていました。
そして2020年にエンジニアリングの博士課程を取得するため来日し、研究に励んでいる頃、KFの社員と知り合ったことをきっかけにインターンの機会をいただき、2022年から新たなチャレンジとしてKFでインターンとして働き始めました。
原子力業界で働いたご経験を持つReubenさんが、フュージョンエネルギーに興味を持ったきっかけを教えてください。
フュージョンエネルギーに強く惹かれるようになったのは、2019年に関わったプロジェクトがきっかけです。
このプロジェクトは、核分裂における化学の領域と腐食に関する知識をフュージョンエネルギーに応用できないかを検討し、その見解を論文としてまとめるものでした。
プロジェクトを通じて、フュージョンエネルギーの実現のために乗り越えなければならない技術的な課題を目の当たりにしました。最初はその複雑さに衝撃を受けましたが、さらなるチャレンジを求めていた私にとって、フュージョンエネルギーは取り組みがいのある非常に魅力的な分野として映っていました。
フュージョンエネルギーに魅了された私は、日本でフュージョンエネルギーを研究している研究室をとにかく探しました。そして材料に関する研究をしている東京大学の教授に直接連絡を取り、腐食を防止するコーティングをフュージョンエネルギーの材料に適用するとどのような反応が起こるのかについて、研究を始めることができたんです。
この研究では高温(840°C以上)と低温(840°C未満)の2つの条件下で材料とコーティングが接する部分の状態を調べました。そして、525°Cで材料とコーティングの接合を可能にする画期的な方法を開発し、材料劣化を大幅に低減することができるようになりました。
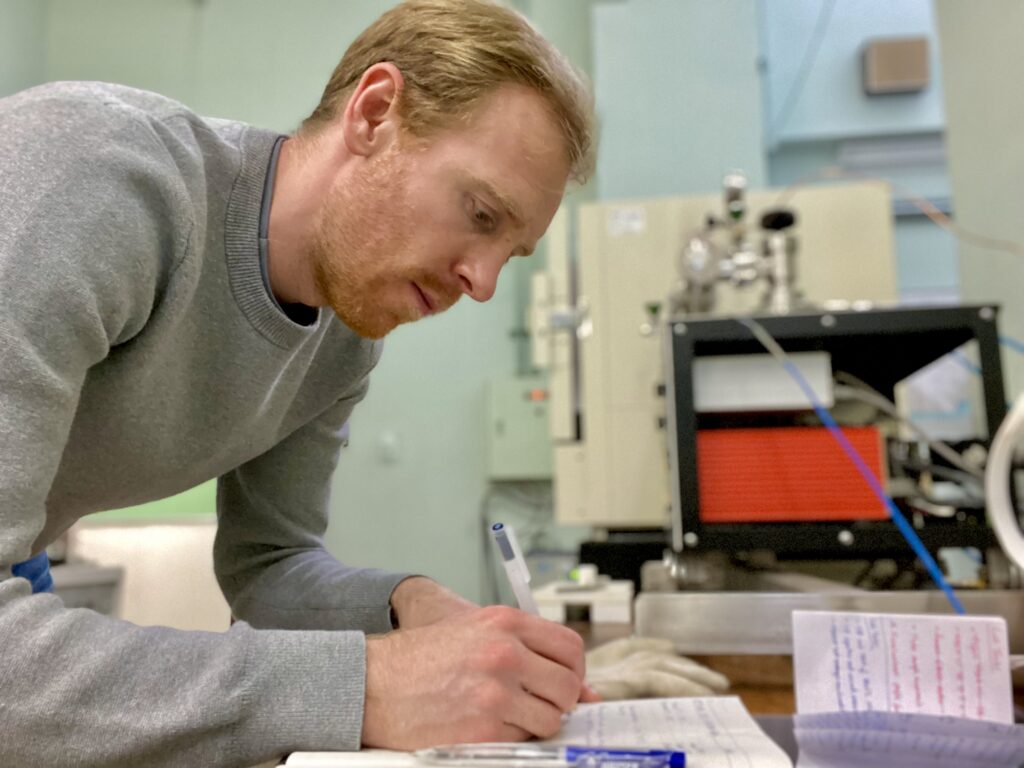
KFは、フュージョンエネルギー関連の材料についてはどのようにアプローチしているのでしょうか?
KFは、フュージョンエネルギーの実用化に向けて、材料の開発と改良を積極的に推進しており、SCYLLA©(Self-Cooled Yuryo Lithium-Lead Advanced)ブランケットのコンセプトに基づき、約1,000℃の高温、放射線、プラズマとの相互作用、磁場、腐食性の冷却材など、フュージョンエネルギー特有の過酷な環境に耐えることができ、かつ経済的にも実現可能な材料の開発に注力しています。
より高い温度で運転を行うと、より効率的な発電につながりますが、一方で材料のさまざまな劣化の原因にもなってしまいます。例えば、温度が上がるにつれて構造材料と冷却材(液体金属、溶融塩、水など)が化学反応しやすくなり、腐食が問題となります。
また、磁場環境も液体金属(LiPb)冷却材の腐食を助長する場合があります。KFでは、こうした材料の劣化が起きるメカニズムをより深く理解することで、フュージョンエネルギー特有の条件下でも、高い耐久性と性能を兼ね備えた材料を開発し、それを用いて安全に稼働するフュージョンエネルギープラントの構築を目指しています。
その目標を達成するために、Reubenさんは日々どのような業務に取り組んでいますか?
私は現在、シニアエンジニアとして論文のデータや実験データをもとに材料の劣化・腐食を調査し、フュージョンエネルギー特有の環境でも使用可能な材料を開発することに取り組んでいます。
核融合炉の運転中だけでなく、製造プロセスや廃棄物処理など、考慮しなければならない点がいくつもあり、日々試行錯誤を繰り返しです。すべての工程において最適な材料の開発は一筋縄ではいきませんが、チームで力を合わせて進めています。
また、性能を向上させる一方で製造コストを削減する方法についても検討しています。積層造形などの先進的な製造技術を利用することで、コストを下げられないか考えているのですが、仮説を何度も立てて検証するも、うまくいかない結果となる場合も多くあります。それでも、材料開発の糸口が見えたときの達成感は言葉では表せないものがあります。
これまで原子力分野で培った経験は、KFでも活かせていますか?
これまで培ってきた材料および腐食に関する知識や経験はフュージョンの分野でも活かせています。ただ、フュージョンエネルギーと原子力の分野では、使用する材料や冷却材が大きく異なるので、新しい材料や冷却材を開発するうえで、フュージョン独自の腐食挙動やメカニズムを理解していく必要があります。例えば、KFでは先端材料(SiCコンポジット)が液体金属(LiPb)と溶融塩(FLiBe)と組み合わせたときに、どのように腐食するのかを研究しています。
未知の領域で仮説を立てながら研究を重ねることは大変ですが、外部に発表できるような成果が得られたときの達成感は計り知れません。実際に研究成果を2023年11月のIAEA主催の技術会議で発表できたときは、とても誇りに思えましたし、研究開発を進め、その成果を発表することで、フュージョンエネルギーの実現に貢献できていると強く実感できた瞬間でもありました。
また、博士課程で得た異なる種類の材料を接合する技術もKFの業務で応用できています。例えば、モリブデン合金で構成された高温熱交換器を開発する際、どのように接合するのかを他のチームメンバーと一緒に検討しています。単にこの材料・構造に適した接合を考えるだけでなく、トリチウムの持つ放射能や冷却材への適合性も考慮する必要があります。材料における課題はKFのUNITY-1やUNITY-2プロジェクトにも影響するので、他のメンバーと密にコミュニケーションを取りながら検討しています。
さらに、Electric Power Research Institute(EPRI)およびVanderbilt University(VU)といった機関との共同プロジェクトにも参画し、安全設計(SiD)手法をフュージョンプラントに応用する研究もEPRI-VUのチームで進めています。このプロジェクトでは、フュージョンプラントで起こりうるあらゆる事故を想定し、設計によって事故の発生リスクをどれくらい軽減できるのかを検討しています。
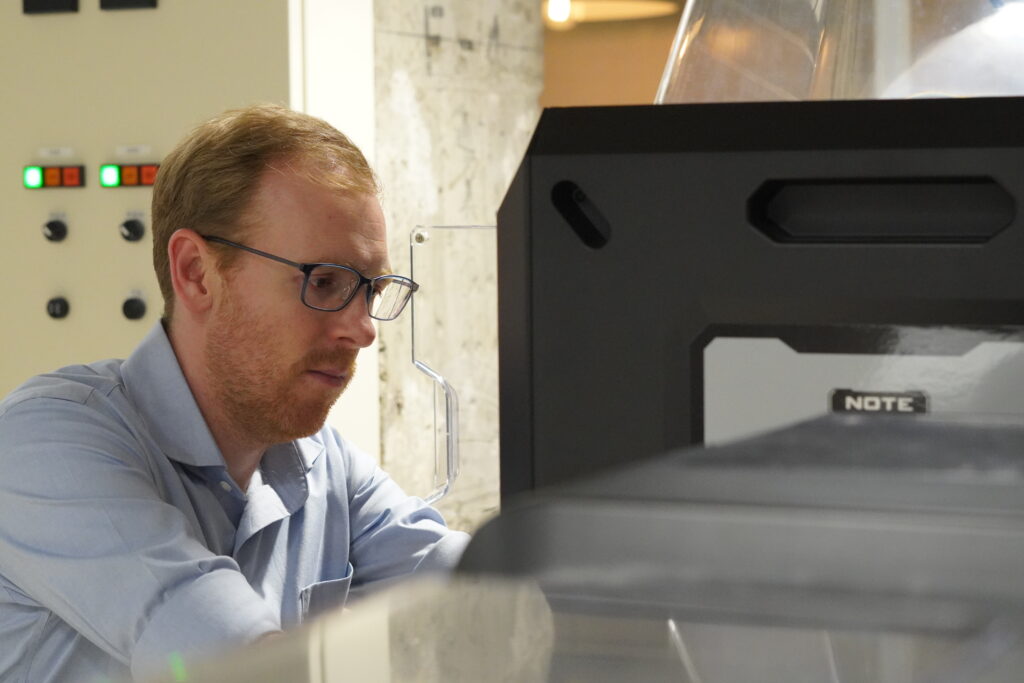
KFでの経験はどのようにスキルや成長機会につながっていますか?
KFで正社員として働き始めてから9か月ほど経過し、スキルアップや新しい成長の機会が得られていると感じます。
KFはグローバルカンパニーとして、海外の学会に積極的に参加しており、私自身も日本だけでなく、オーストリアやイギリス、アメリカなど、世界中の学会で発表を行う機会を得ることができました。
実は、私はもともと人前で話すのが得意ではなかったのですが、こうした国際的な会議や学会に何度も参加し、専門家の前で話すうちに自信がついてきました。次第にもっと活躍したいという思いから、the ASME Special Working Group for Fusion Stakeholders (SWGFS)の委員に応募したところ、なんと任命されました!
これからは、より俯瞰的な視点を持って、フュージョンエネルギー業界全体を実現に向けて前進させ、それに必要な材料の基準策定やコミュニティ支援のためのツール構築に尽力したいと考えています。
最後に、Reubenさんが思い描くフュージョンエネルギーの未来と、KFで達成したい目標を教えてください。
私が生きているうちに、フュージョンエネルギーの発電プラントが実装され、商用化が実現すると強く信じています。一方で、その道のりにある数々の課題があることも事実です。
フュージョンエネルギーの実用化を目指す上で、日本や海外で豊富な経験を積んだ研究者やエンジニアが集まり、技術開発に強みを持つKFはとても魅力的な職場だと思います。これまでに蓄積されたフュージョンエネルギーの研究成果や技術をもとに仕事できており、感謝しています。
また、私の個人的な目標は、技術面での挑戦に加えて公正で誠実な組織文化を醸成することです。一人ひとりが最高のパフォーマンスを発揮できる環境を作ることで、KFのさらなる成長につなげられたらと思っています。