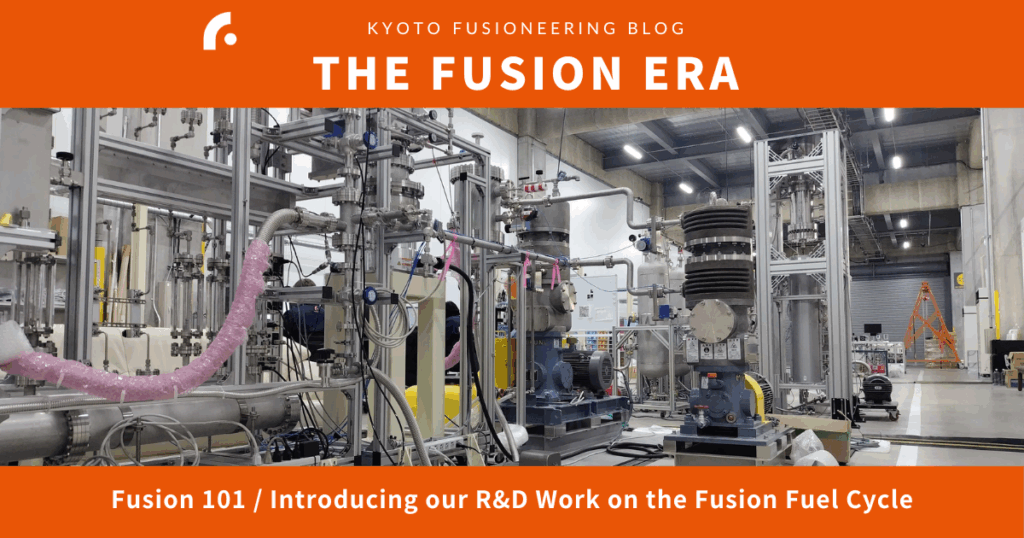
KF’s new headquarters, which opened its doors this January, houses both our R&D facilities and our offices. In a previous post, we introduced the office space, and this time, we’re diving into the R&D facilities to give you a firsthand look into the kinds of development taking place there.
– The “Fusion Fuel Cycle System” – Essential for Fusion Power Plants
The practical application of fusion energy requires continuous operation. This means fusion reactions must be sustained, requiring a constant supply of fuel to the fusion reactor. That’s where the Fusion Fuel Cycle System becomes an important technology.
When generating deuterium-tritium (D-T) fusion reactions—considered the most achievable type of fusion—most of the fuel injected into the reactor does not actually undergo fusion and instead remains within the reactor. Since tritium is an extremely rare element, simply exhausting it would quickly lead to a fuel shortage. To ensure a consistent fuel supply, the fusion fuel cycle system extracts only the deuterium and tritium from the exhaust gases of the reactor and recirculates them for reuse.
Fusion fuel cycle systems comprise the integration of multiple pieces of equipment and systems, including special pumps to transfer the exhausted gases. Certain pumps allow only hydrogen to permeate, and others use chemical reactions to facilitate the recovery of fuel elements.
At our facility, we are conducting performance tests on individual components and systems. These will eventually be integrated into “UNITY-2*” for full-scale testing in the future.
*Note: Construction is underway at Chalk River, Ontario, Canada, led by Fusion Fuel Cycles Inc., a joint venture with the Canadian Nuclear Laboratories, to conduct real-world integration tests using tritium.
– A Peek Inside our R&D Facilities!
This section introduces key aspects of our R&D facilities. It’s important to note that no experiments using tritium or other radioactive substances are conducted here.
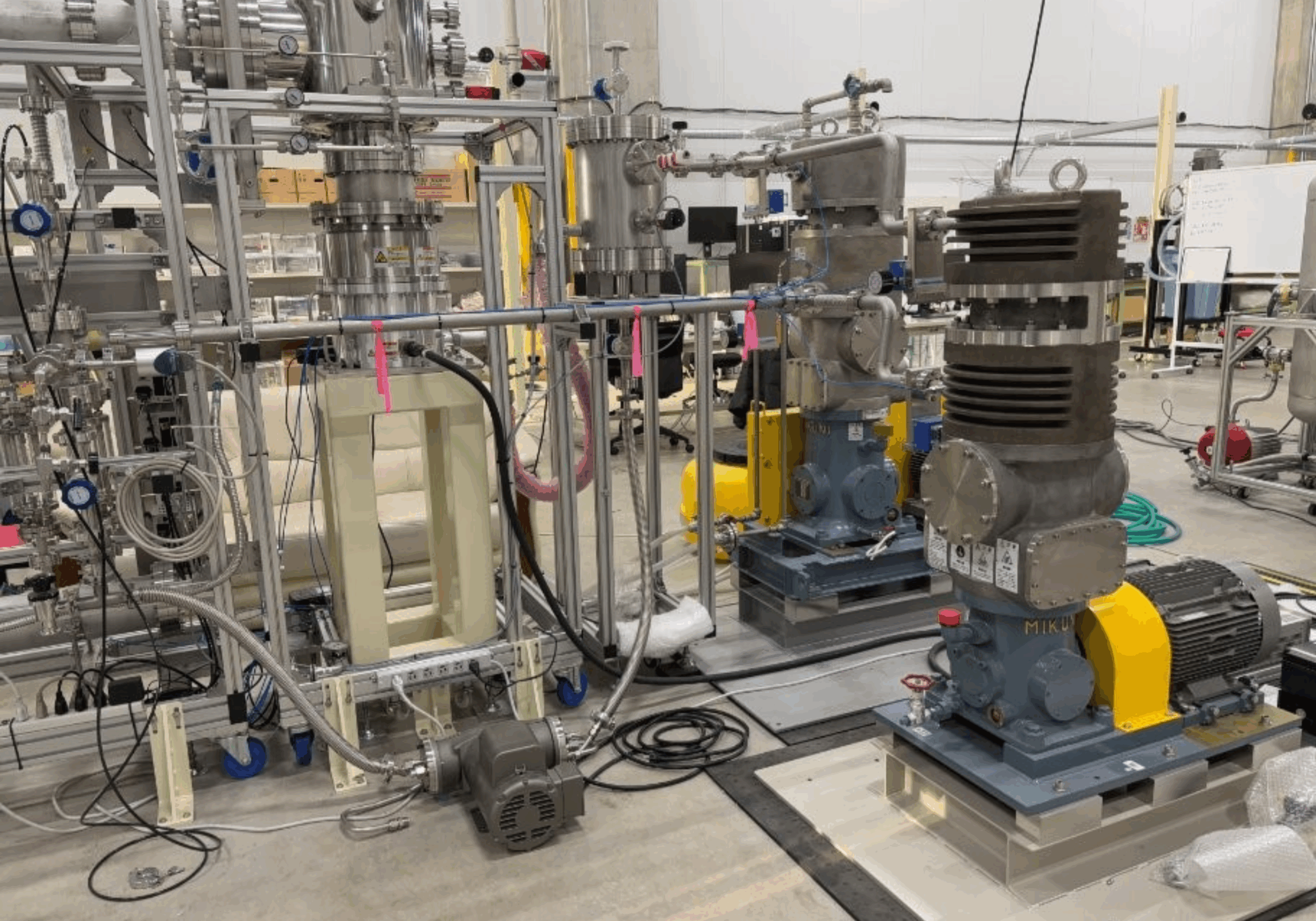
First up are pumps—essential components of the fusion fuel cycle system. They’re used to extract and transfer gas from the vacuum environment inside the fusion plant. The vacuum pump developed with MIKUNI JUKOGYO CO.,LTD. is highly durable against radioactive materials and has excellent exhaust performance, even for light gas species like hydrogen. We’re also testing the performance of a combination of other pumps, including turbo molecular pumps and metal bellows pumps.
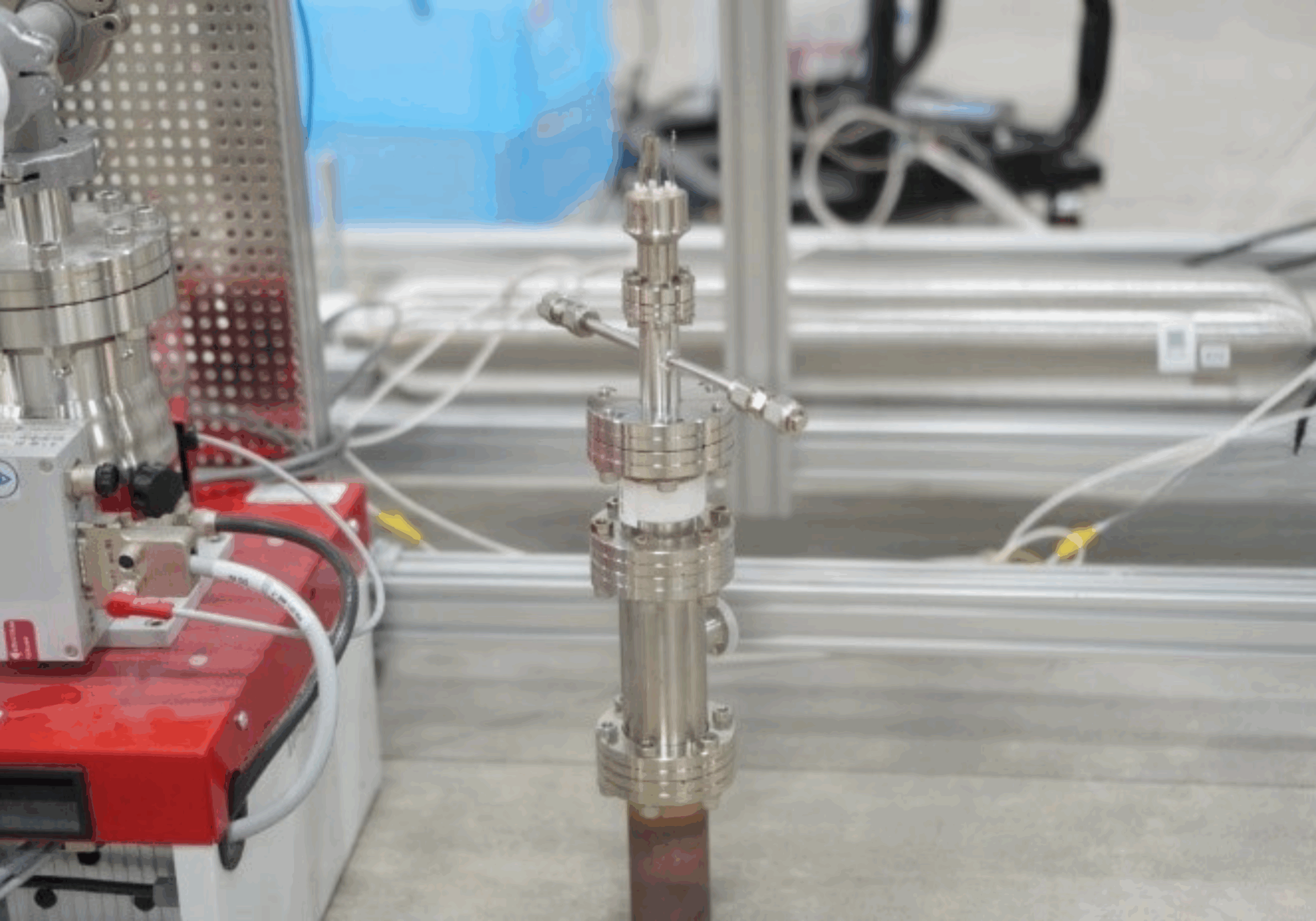
The next piece of equipment, a storage unit, is used to store recovered fuel. It stores deuterium and tritium that have been separated and recovered from exhaust gases, and supplies fuel when needed. The hydrogen is absorbed and stored in ZrCo (zirconium cobalt), a hydrogen storage alloy. We are currently testing the optimal temperature and pressure conditions for actual hydrogen storage.
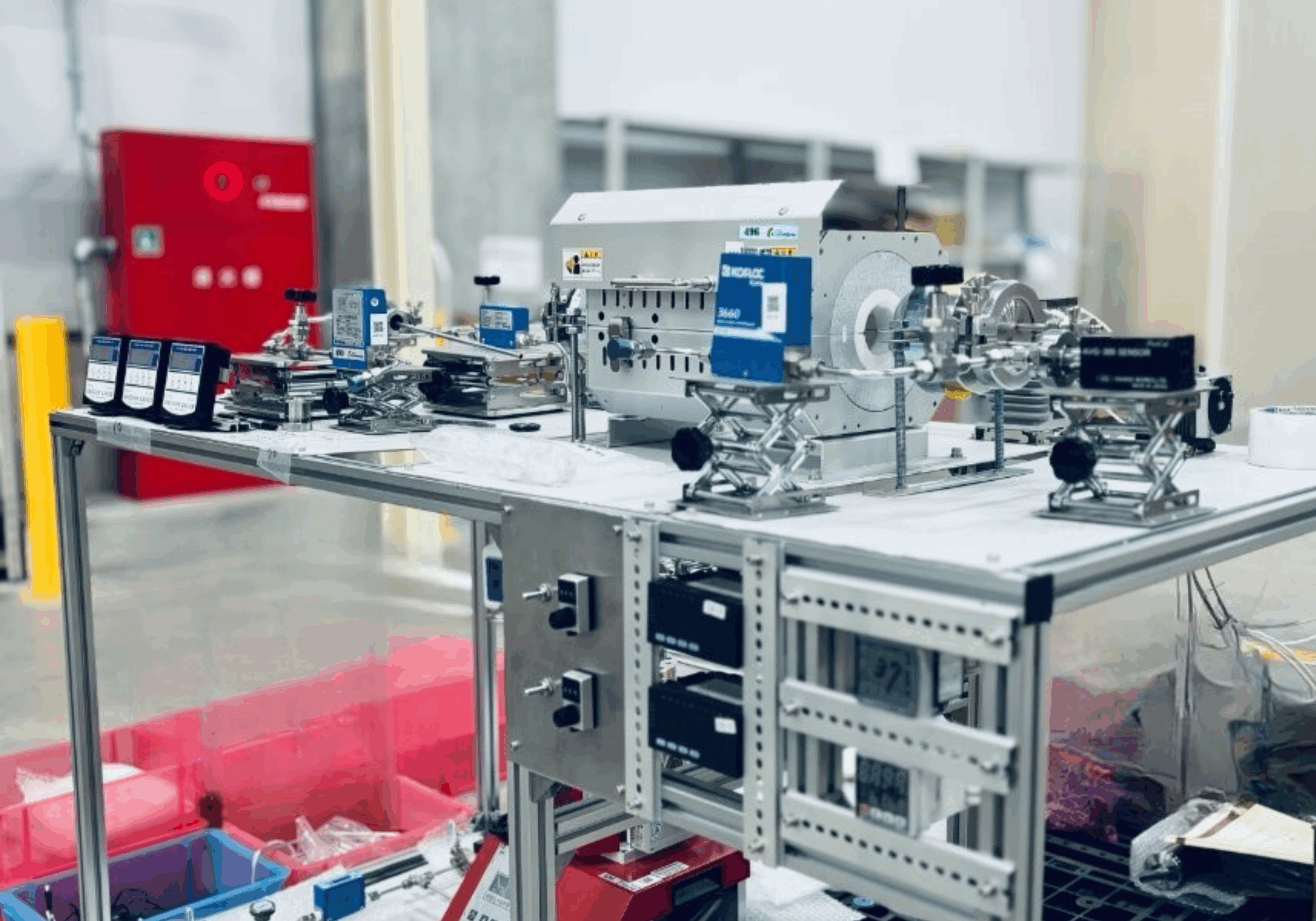
We’ll now look at a Proton Conductor Pump. This pump uses a proton conductor, which can selectively extract hydrogen isotopes from the gas discharged from a fusion reactor. We’re testing its performance to selectively transfer hydrogen and deuterium.
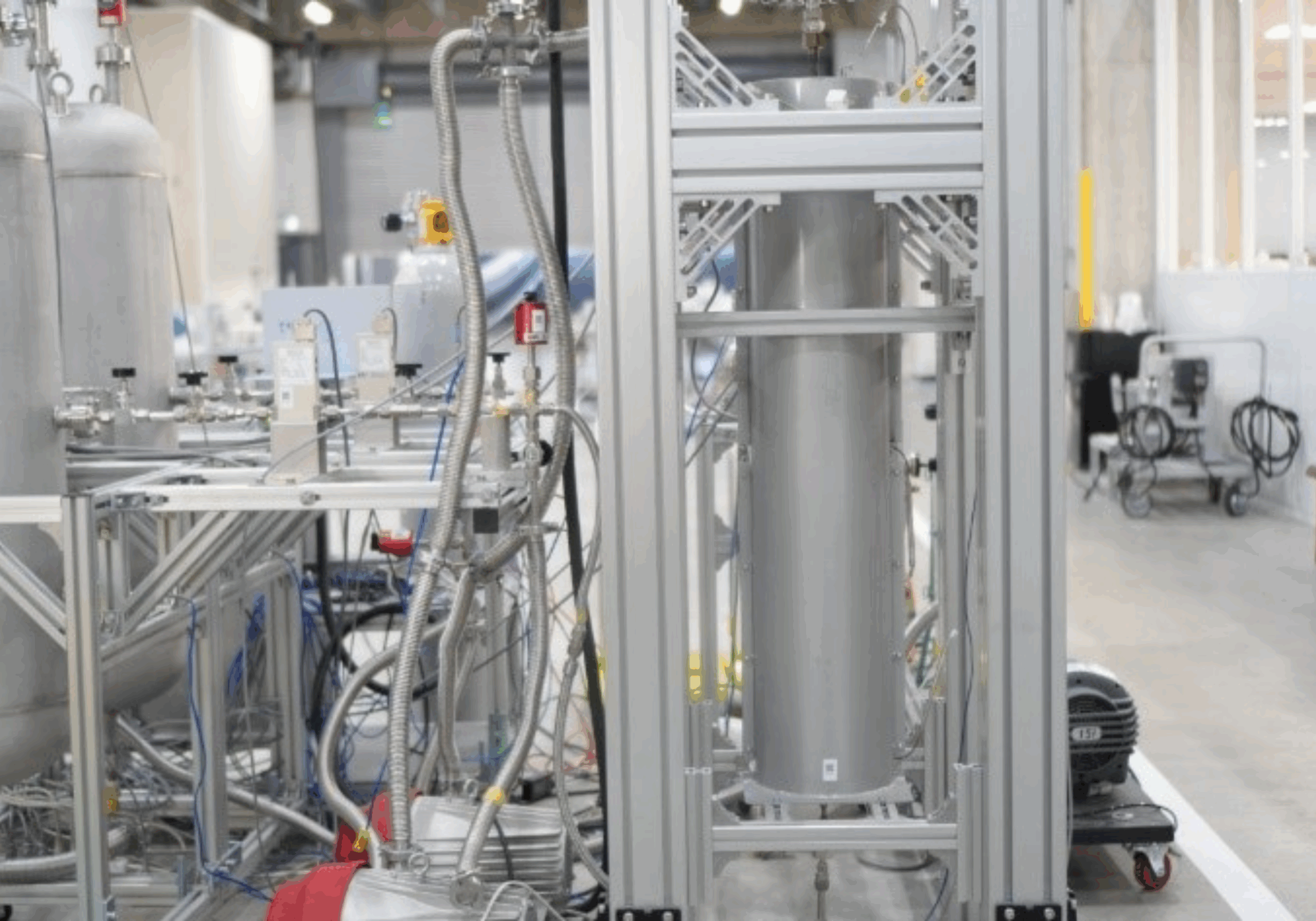
Next, the Palladium Diffuser recovers hydrogen isotopes selectivity from gases including impurities gases emitted from the fusion reactor. This system takes advantage of palladium’s selective permeability to hydrogen gas. We’re conducting performance tests to evaluate its ability to recover only hydrogen isotope gases from the exhaust stream.
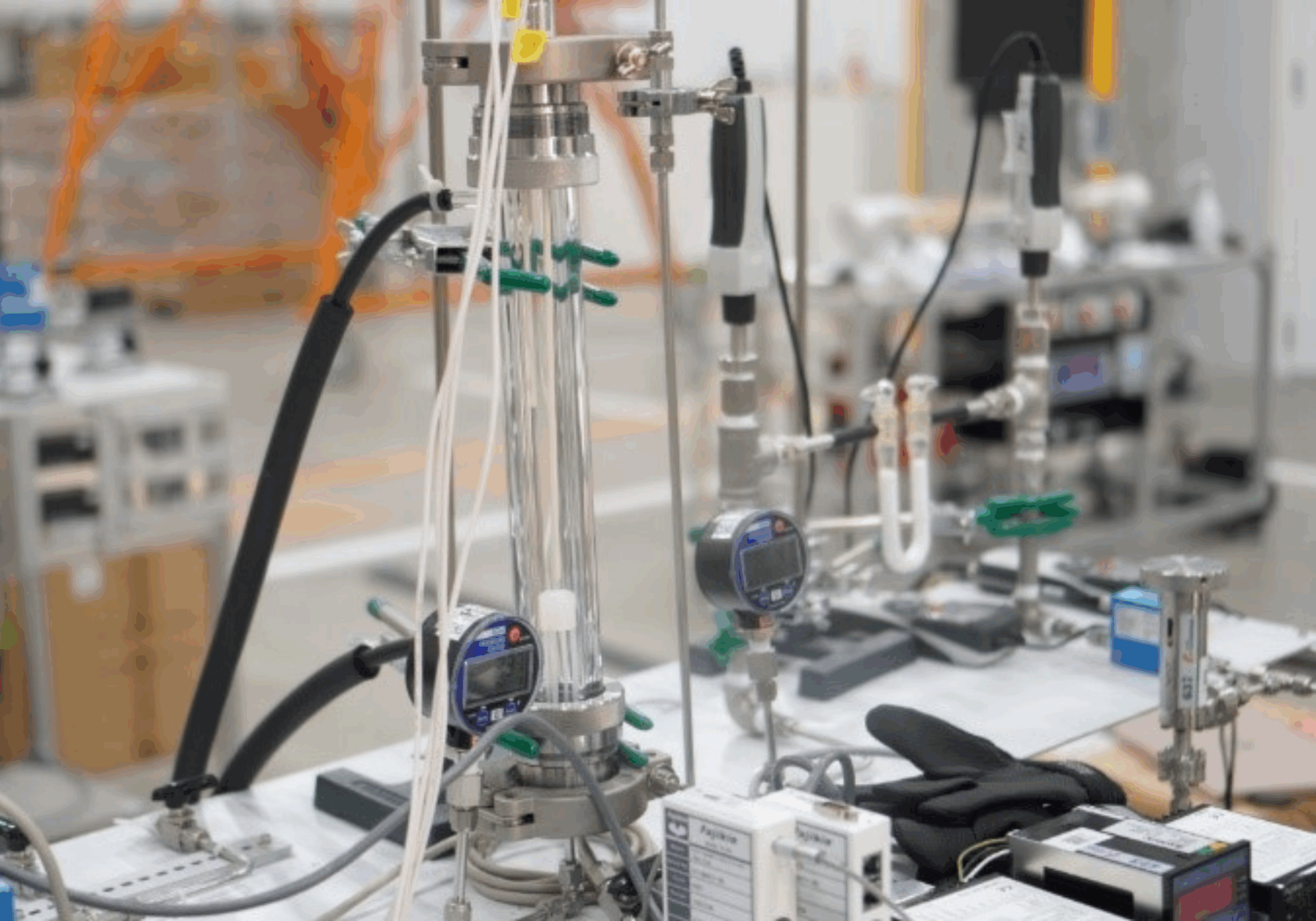
Last but not least, the Water Detritiation System (WDS). Water containing tritium is generated in the process of separating the gas emitted from the fusion reactor. The WDS separates tritium from the water to reuse the tritium and ensure water is safely released into the environment. Currently, we are testing separation performance using steam mixed with hydrogen.
This concludes our introduction to key systems. We’re also developing other essential components for the fusion fuel cycle, including devices for separating hydrogen isotopes and tritium measurement instruments.
UNITY-2, which integrates all of these systems, is scheduled to begin operations in 2026. Engineers in the Plant Technology Development Division are working daily on performance testing and other activities in preparation for this.
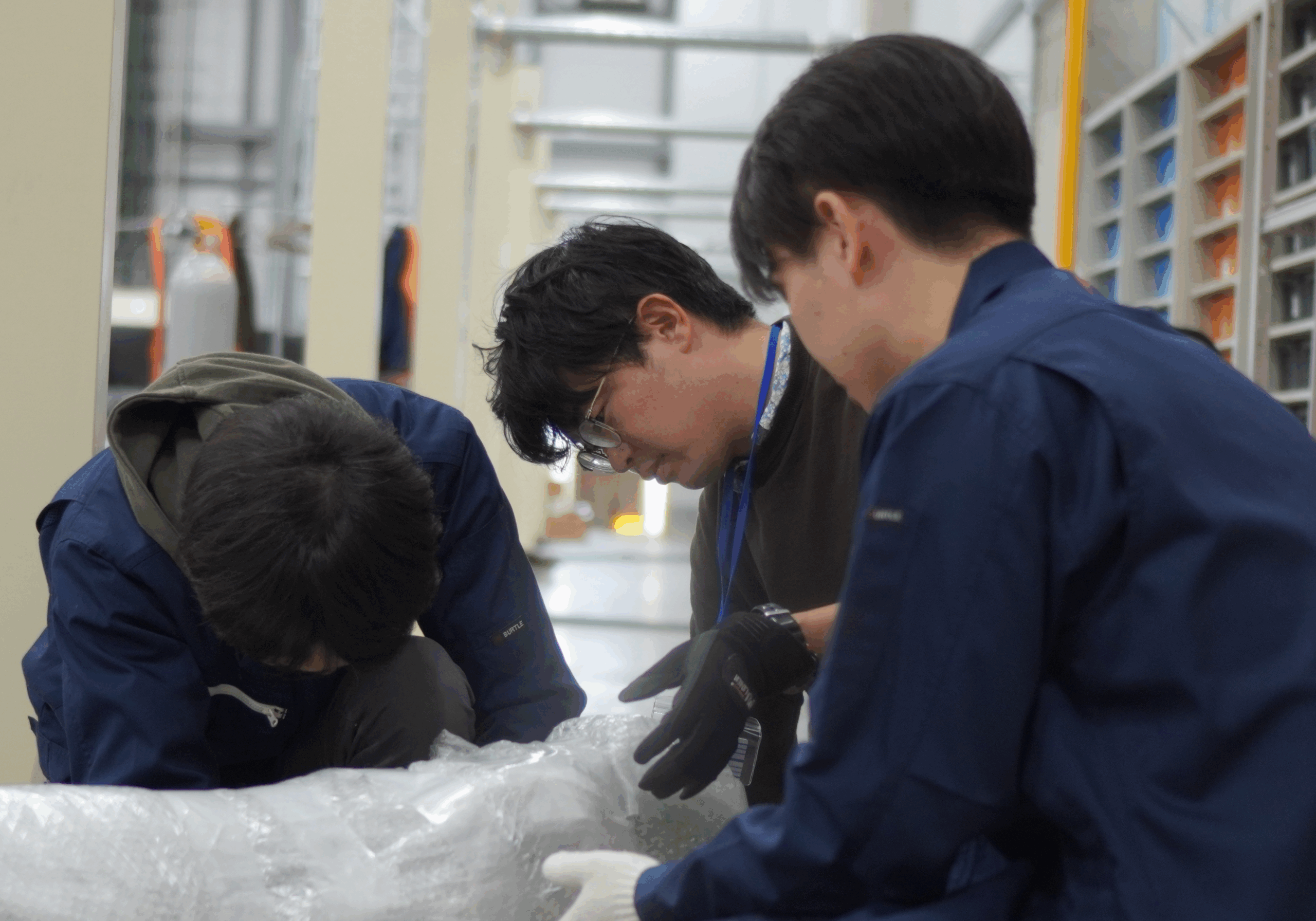
In this blog post, we shared a glimpse into the R&D facilities for the fusion fuel cycle system — a key technology that will play a crucial role in making fusion energy a reality.
Stay tuned for a future post where we’ll introduce our dedicated engineers working tirelessly behind the scenes!
Subscribe to Our Newsletter (LinkedIn)