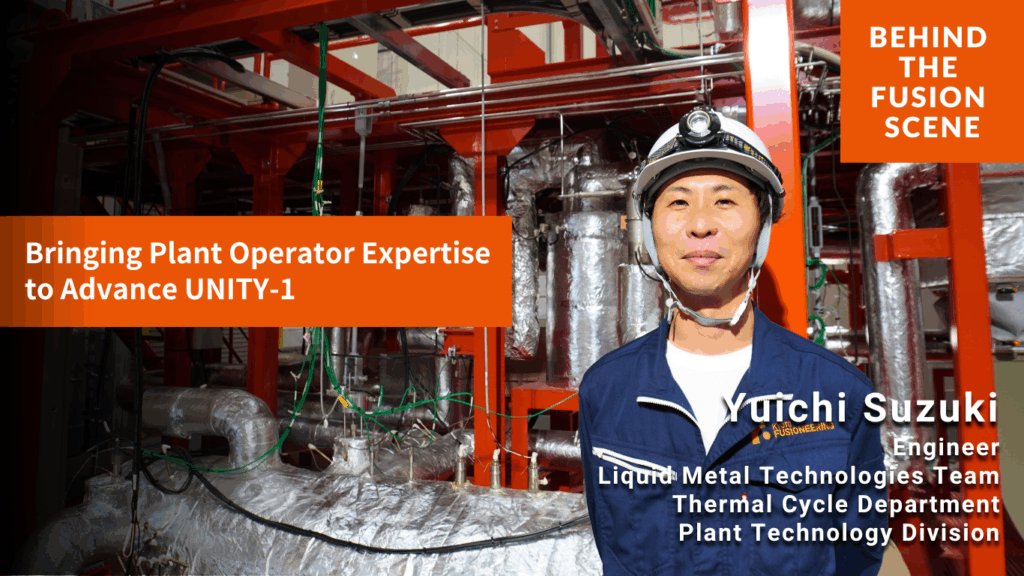
In a nutshell:
Yuichi Suzuki joined Kyoto Fusioneering (KF) in June 2024. He serves as a plant operator for UNITY‑1, our state-of-the-art fusion energy demonstration plant to test advanced power generation techniques. With a solid background in chemical and natural gas plant operations, he oversees pre‑test environment preparation and equipment control. His hands-on expertise is helping bridge conventional plant operations with the future of clean fusion energy.
You’re now working as a plant operator at Kyoto Fusioneering (KF)–have you always been drawn to engineering?
I got my start in engineering in my mid-20s. Before that, I worked in the beauty industry as a distributor, selling hair dye and perm products to salons. That job was rewarding in its own way, but as I began thinking more seriously about my long-term career path, I found myself drawn to something more technical. My dad worked in the electrical field, and his influence played a big part in sparking that interest.
I then decided to apply to several companies offering technical roles. I landed a position as a plant operator at a facility that used dimethyl ether (DME), a clean, easy-to-handle next-generation fuel. That opportunity marked the beginning of my journey into the engineering world.
After making the leap into engineering, what kind of experiences have you had?
About three months into the job, the DME demonstration plant was scheduled to go live—and as the plant operator, I was expected to be hands-on at the site. That meant I had just three months to learn the basics of plant operations and fully understand the plant’s design and specifications. It was intense, to say the least.
Coming in with almost no background in machinery or chemistry, I found it tough at first. I struggled to keep up with conversations among senior staff, and reading technical blueprints felt like decoding a foreign language. Even though I received a lot of feedback from my supervisors, I remained motivated because I was truly fascinated by the work. DME plants were still cutting-edge at the time, and I kept thinking, “It’s incredible that people can conceive of these frontier technologies and turn them into reality.” That sense of wonder and purpose helped carry me through the challenging days.
You really dove into the world of plant operations after your first role—what came next?
While working hard to get up to speed, I also began earning certifications to deepen my knowledge. That momentum led me to my next role: operating control systems at a commercial LNG (liquefied natural gas) plant.
There, my responsibilities expanded significantly—adjusting output to match regional demand, planning high-pressure gas maintenance (critical for safety), drafting construction specs, and prepping equipment for inspections.
Unlike the hands-on work I did at the DME plant, this time I was also operating the DCS (Distributed Control System). It was challenging, but I could feel myself growing into the role. With each new responsibility came a real sense of progress and reward.
Later on, I joined a company focused on next-generation biofuels, working on bio-JET and biodiesel plants. That experience helped me refine my skills even further—and deepened my passion for energy innovation.
What have been your biggest challenges—and most rewarding moments—as a plant operator?
The toughest part has definitely been the constant pressure. Even during routine operations, we’re always on alert—monitoring daily data and test targets, while staying ready for the unexpected. If anything goes off course, we have to react immediately to prevent emergency shutdowns.
At the LNG plant, the stakes were even higher. A shutdown there could impact people’s daily lives, so there was zero room for error. I remember times when natural disasters or power outages forced unplanned stops, and we had to safely shut down—or restart—extremely complex systems under irregular conditions. It was high-stakes, high-concentration work.
There was one stretch in my career when our team faced a wave of operational issues. Morale dropped and people were asking, “Can we really pull this off?” But we didn’t give up. We came together, shared ideas, refined our processes, and over the course of 18 to 24 months, we delivered successful bio-jet and diesel fuel production. That moment of triumph—after so many trials—was unforgettable. While there were challenges along the way, being part of a team pushing the boundaries of next-generation energy technologies was incredibly meaningful. The feeling of reaching a milestone after all the trial and error—there’s really nothing like it.
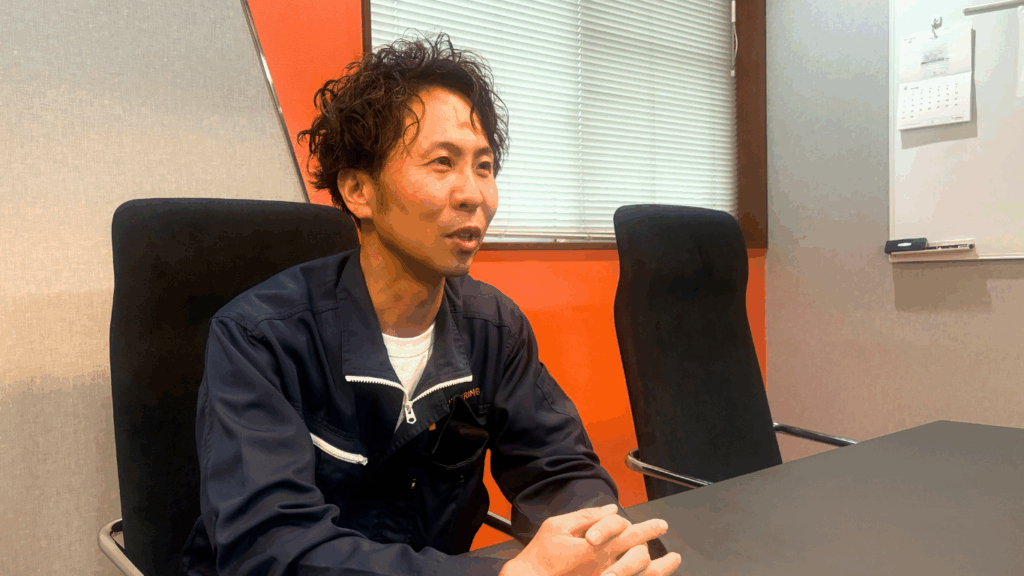
What motivated you to join Kyoto Fusioneering (KF)?
I’ve always been driven by the challenge of taking on something new and pushing toward meaningful goals. I also wanted to play a more active role in the development of next-generation energy. While exploring opportunities, I came across KF and its mission to advance fusion energy. At the time, I only had a vague idea of what fusion was—but the more I learned, the more I thought, “If this becomes reality, it could truly change the world.” That sense of possibility was incredibly exciting.
When I saw the job posting, I hesitated at first—“Do I really have the skills to contribute?” But my interest in fusion energy kept growing, and I knew I’d regret not trying. I reminded myself, “Nothing happens unless you take the first step.” So I applied—and was lucky enough to be given the opportunity.
Since joining KF, what have you been working on?
I’m currently the plant operator for UNITY‑1, located at our Kyoto Research Centre. UNITY‑1 is a cutting-edge R&D facility that has already run test operations involving liquid metal circulation and hydrogen isotope extraction using the Vacuum Sieve Tray (VST) system—a key step in developing the fuel for fusion energy.
My role includes preparing the site before tests, operating the equipment, and monitoring system performance throughout each run. If something seems off—like an unexpected reading or a sudden equipment stop—I document the situation immediately, report it to the team, and we work together to find a solution. I also help translate essential testing procedures into operating manuals and troubleshooting guides, keeping them up to date as our systems evolve. In addition, I prepare for future expansion of equipment by maintaining daily organization and cleanliness within the plant, including tidying up supplies and keeping the workspace orderly to ensure the safe operation of UNITY-1.
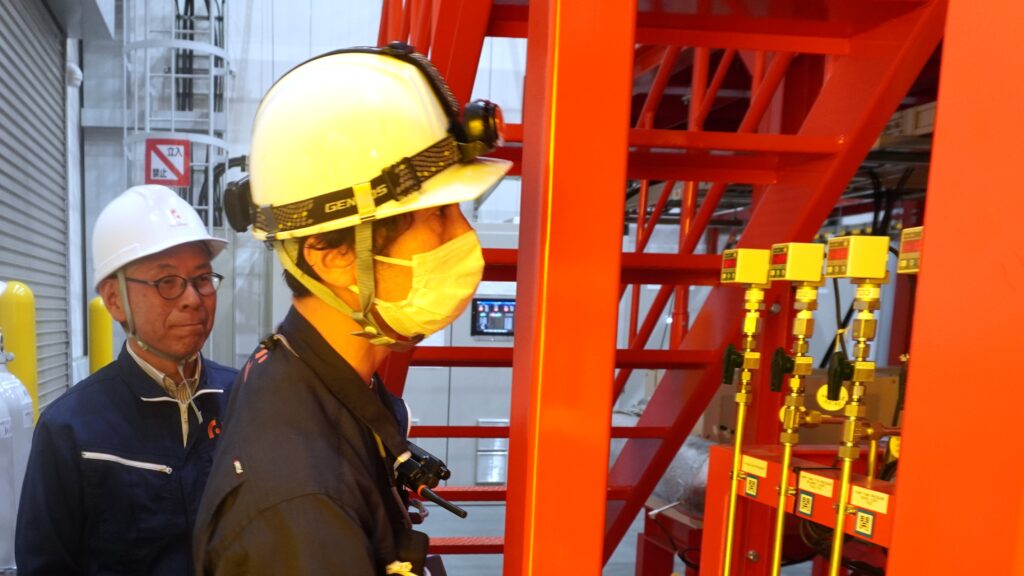
What makes UNITY‑1 especially exciting is that it involves fusion-specific fluids and technologies I have never encountered before. Conventional plant know-how doesn’t always apply here. We need to prevent liquid metal from solidifying in the pipes, assess magnetic field effects during MHD pressure-loss tests, and manage a complex range of systems and conditions.
It’s a steep learning curve, but I rely on my past experience with next-generation energy plants and collaborate closely with our incredible team. UNITY‑1 is aiming to be the first facility in the world to demonstrate fusion power generation technologies in a simulated environment—and I’m proud to be contributing to something so groundbreaking.
Watching UNITY‑1 evolve since my very first day has only deepened my belief that KF is playing a vital role in accelerating the realization of fusion energy—driven by homegrown Japanese technology.
Finally, what do you hope to achieve at KF?
I see my mission as helping to optimize and standardize our operating techniques and equipment—making sure that systems like vacuum pumps and power-generation units can run reliably and efficiently over the long term.
At the same time, I want to keep sharpening my own technical skills and knowledge, contribute to the successful demonstration of UNITY‑1’s power-generation technology, and ultimately play a part in bringing fusion energy from concept to reality.