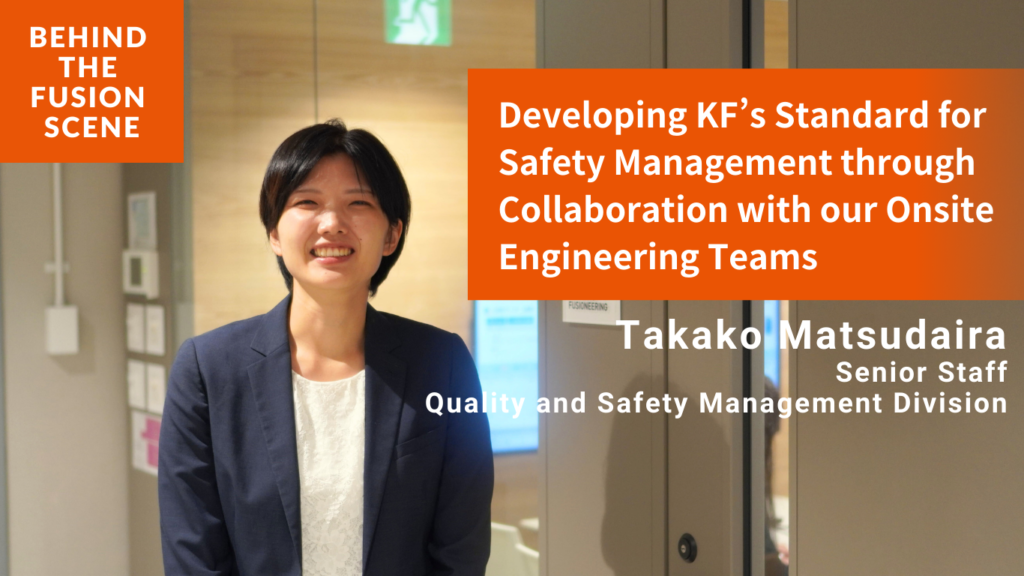
In a nutshell:
Takako Matsudaira joined Kyoto Fusioneering (KF) in December 2023 and leads safety management across the organization, including at the Kyoto Research Centre, our first in-house development facility.
She is making a significant contribution to safety by overseeing how KF formulates and implements safety rules that reflect the actual situation on the ground. She does this by leveraging her knowledge base and communication skills that she has acquired in her career to date.
Could you tell us more about your work at KF?
I lead the overall safety management of sites involved in R&D and experimental work. Since there are so many potential risks in the field of technological development, I am working to create a system that will minimise any potential risks in advance, and also enable us to respond swiftly in the event of an emergency. The Kyoto Research Centre (KRC), our first in-house development facility, began operations soon after I joined KF so we needed to create safety management policies from scratch. While I had worked on safety management in my previous position, this was my first time setting up a completely new system. I did feel some pressure, but at the same time, I saw this as a new challenge and approached it with a positive mindset. I have developed both the policies and the training for the engineering staff so that each member keeps the guidelines they need to follow in mind on a day-to-day basis.
How exactly have you been working on creating the policies?
While the basic safety policy was already in place when I joined KF, we needed to carefully look over and update the content to suit the situation on the ground at our development facility. With the UNITY-1 now installed at KRC, we will be carrying out simulated power generation demonstrations and handling high-temperature liquid metals. We have also been talking to and consulting with the local government, fire station and public health centre where KRC is located to ensure that the local community is aware of our safety procedures. This includes sharing information and completing the necessary paperwork while integrating the new safety policy with already existing procedures. We spared no effort, even making repeated visits to explain key points to each of the relevant organisations, because safety should take the highest priority.
As an example, since a large overhead crane is needed to build UNITY-1, a large-scale installation, we have developed procedures (including requiring the crane to be reserved in advance and displaying warning notices) to ensure the safety of the surrounding area when the crane is in operation, and have set up restricted access zones. We also anticipated that many people would visit the facility, so we prepared new safety guidelines for visitors, and created inspection and maintenance checklists to be displayed at the site. Starting from basic safety measures, we developed a comprehensive safety package for our development facility.
We also recently created policies for unmanned night-time operations to fit the actual conditions on site. We built a system for checks and approvals while adapting to the scale of the equipment and the surroundings, which required consistent communication with the engineers on site. I felt a strong sense of achievement since we were able to develop company-wide KF standards that included measures for what to do in the event of an emergency, as well as how to ensure safety without impacting the ongoing experiments.
How did you ensure that the employees integrated these safety procedures into their work?
We held in-house training sessions on safety and set up regular opportunities for information sharing. During the in-house training sessions, I explained why these safety measures were necessary and provided the rationale behind them. I also tried to explain in concrete terms what people should be careful about in their actual work. Also, because I had realized from past experience that people wouldn’t always integrate this information, I adapted the training to make sure that participants could visualise what may happen at the actual site and used quizzes, images and videos to enhance the content.
We also shared information by bringing together the on-site engineers and the management team on a weekly basis to go over the upcoming work schedule in advance. By sharing and checking on the kinds of work involved in conducting experiments and constructing the facility, we are able to prepare in advance and issue reminders to team members on-site. I was a little concerned that checking every little thing in detail might be too much, but I think it’s been helpful overall since we’ve been able to share important information and learn a lot from our engineering team.
When there is work to be done on site, we always share what we will be doing and what requires extra caution for our on-site members before the work begins. During the monthly on-site safety patrols, we check to see if the work is being carried out properly and if there are any potential areas of caution. When countermeasures are needed, we add them to the safety policy.
At the moment, the safety policy is based on the work carried out at our one in-house R&D facility, but I think that the safety procedures we have developed there can be applied to other facilities that we set up in the future. While we would need to take into account different factors, like R&D project specifications and local laws, I’d like to make our safety policy as standardised as possible and ensure that it is fully integrated within KF.
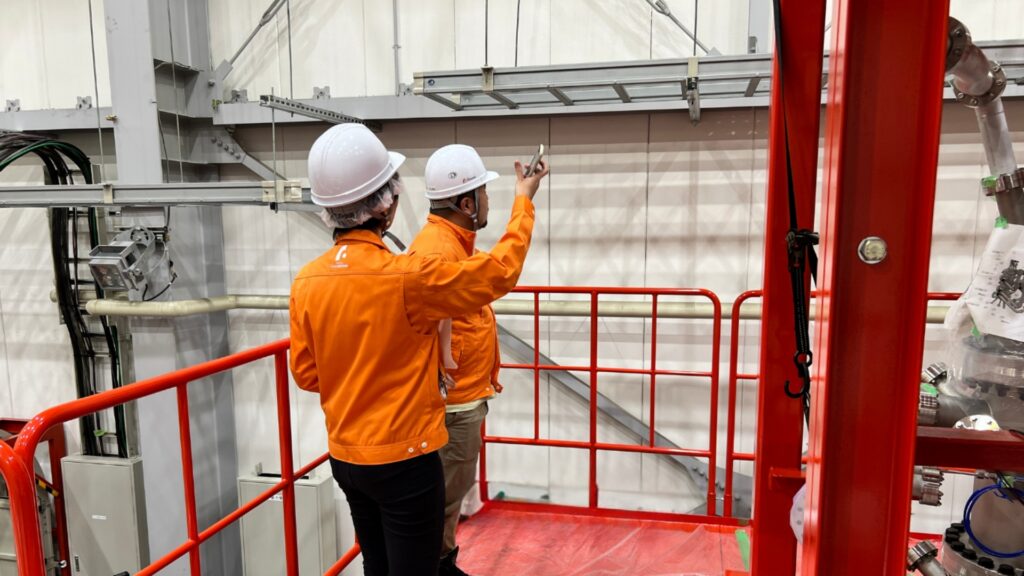
Satoshi Ogawa (back right), the site head, works with a member of the safety patrol team (front left)
Could you tell us more about your career to date, including your previous work in safety management?
I joined a metal materials manufacturer straight out of university and worked in quality assurance. This department communicated with customers about deliveries, but depending on the nature of the enquiry, I went out to the production site from time to time to conduct interviews or carry out investigations in the factory. I’ve always liked looking at machinery like experimental and production equipment, so my curiosity was often piqued by the work I did on site.
After changing positions, I ended up working closer to the production floor than before and got involved in creating quality control standards and carrying out daily quality inspections. As part of my work in safety management, I listened to those working on the production floor, and based on these experiences, I was able to put into practice multiple approaches to ensuring safety. I’m able to apply my experiences from this previous role to my current work at KF.
Since you began working for a metal materials manufacturer straight out of university, did you study science-based subjects at school?
I majored in chemistry at university, where I studied theoretical computational fields. When deciding on a career path, I felt that a research-focused career would not be an ideal fit, so I decided to work full-time after getting my degree. As a science major, I was interested in manufacturing, so I had my mind set on working for a manufacturer. I chose to work for a metal materials manufacturer since this field is related to chemistry, and since I was familiar with this industry through a fellow student’s research on metallic materials.
As a slight aside, I was originally interested in biology, so I actually applied for programs in both biology and chemistry. I have always liked insects, and I enjoyed catching them with my grandparents when I was a kid. I still like biology, but I think it was fortuitous that I ended up going into chemistry and then joining KF.
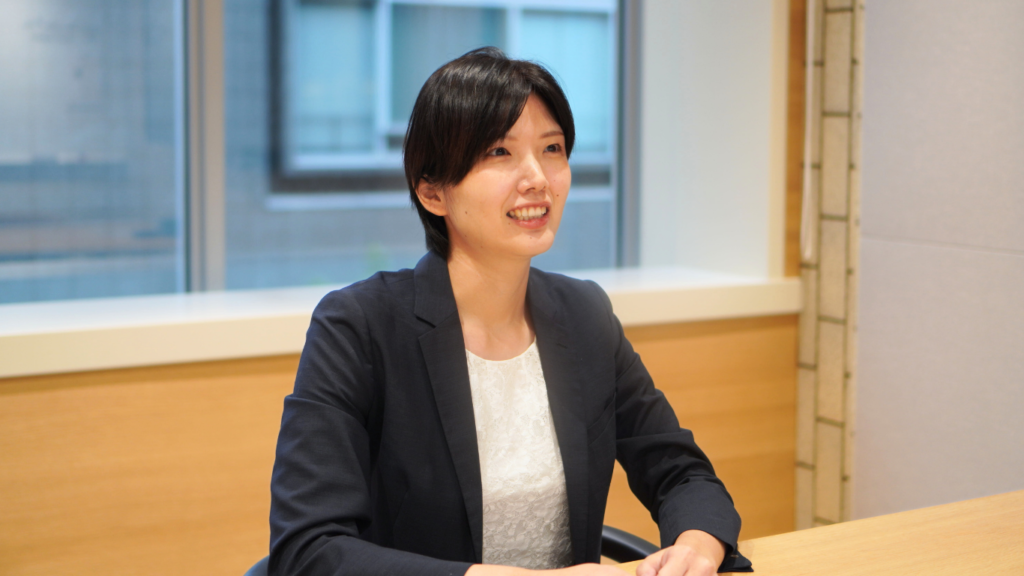
How has your experience with Fusion and KF been?
Upon returning to work after parental leave at my previous job, I was looking for an environment where I could better balance work and family life. I was introduced to KF by a recruitment agency right at that time, which was my first encounter with fusion and KF.
The recruiter thought that I would be a good fit based on my career in safety management, but since I knew very little about the industry or the company, I started doing some research. I had been involved in the energy sector in my previous job, so it was very interesting for me to gather information on this area. I was excited by the prospect of working on a large-scale project to develop a new energy source. I also thought about how critical manufacturing technology is for this sector and also how this would fit well with my own interests. Also, having worked for well-established companies up until now, I was attracted by the prospect of working in a different environment like a venture or startup. In terms of my career, I was expanding my work beyond quality control to include safety management, so I was hopeful that I could specialise in safety management at KF.
Through the interview, I was able to get a good idea of what was expected of me and what I would be doing after joining the company. In learning more about the work environment, I discovered that many employees took a flexible approach to work while also taking responsibility for their tasks.
When I received the job offer, I debated between gaining more experience at my previous position or taking on the challenge of working in a new industry. Ultimately, with some nudging from my family, I decided on taking the position at KF for 3 reasons: I would be a part of an organization working on the future of energy for the benefit of humanity, I could leverage my previous experience in the manufacturing sector, and I could work flexibly, which suited my lifestyle. Right from the start, I was busy travelling between the Kyoto facility, which had just been set up, and the Tokyo office, but I am ultimately glad that I chose KF because I am able to take on new challenges by working on safety management from the ground up and I’m making use of my previous experience.
Finally, what would you like to achieve at KF in the future?
First of all, I would like to establish a standard safety policy for KF. We also need to establish procedures that are unique to fusion development facilities. To do so, it will be essential to harness the knowledge of those who have been involved in fusion research and technology development for many years. Fortunately, many experienced researchers and engineers, as well as experts in their fields, work at KF, and many of our engineers have worked in research institutes and large companies. I think that one of KF’s strengths is that we can incorporate a variety of perspectives, so I would like to integrate the voices of those on the front line and create safety management that is in line with what is happening on the ground. To do this, we need to strengthen our understanding of what is happening on the front lines, so I would like to continue to regularly communicate with engineers and other on-site members while continuing to learn more about fusion.